Understanding the different types of plastic is important in everyday life. Different types of plastic have different properties and recyclability, which helps us make informed decisions about the products we use and their impact on the environment. In addition, understanding the types of plastic can also help avoid potential health risks. In this article, we will learn about the 8 most common types of plastic used in manufacturing and life.
I. PET (Polyethylene Terephthalate)
Polyethylene Terephthalate, also known as PET or PETE, is a type of plastic commonly used in the production of beverage bottles, food packaging and clothing fibers.
PET is a versatile material that is lightweight, durable and resistant to moisture and chemicals. It is also easily recyclable, making it an environmentally friendly choice for packaging and other products.
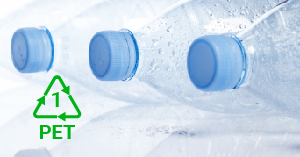
II. HDPE (High Density Polyethylene)
High density polyethylene (HDPE) is a rigid plastic used to make plastic containers. HDPE is commonly used for bottles containing cleaning products, cosmetics, and toiletries; it is also used to make milk bottles, plastic pails, and buckets. The rigidity of HDPE makes it ideal for wear-resistant plastic products.
HDPE is also used in the production of products that require resistance to high temperatures and harsh environments, and in the construction industry for pipes, fittings, and geomembranes.
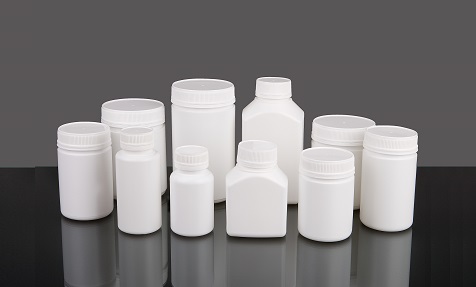
III. PVC (Polyvinyl Chloride)
Polyvinyl chloride is a versatile and widely used plastic material. It is a thermoplastic polymer produced through the polymerization of vinyl chloride monomers.
PVC is commonly used for flexible and rigid plastic products, such as pipes, vinyl flooring, and window frames.
One of the main advantages of PVC is its cost effectiveness. It is an affordable material that offers long-lasting performance, making it a preferred choice for many industries.
However, it is important to note that the production and disposal of PVC can have health and environmental impacts. PVC can release toxic chemicals when burned.
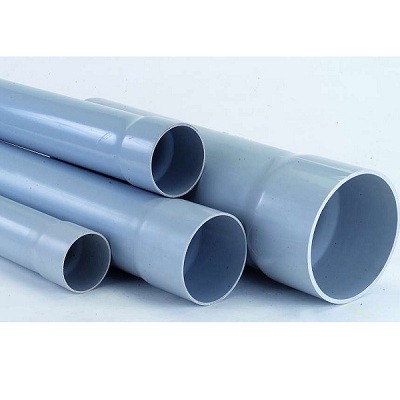
IV. LDPE (Low density polyethylene)
Low density polyethylene (LDPE) is one of the sub-branches of PE plastic. LDPE is a soft plastic, commonly used to make plastic bags, candy wrappers, and cosmetic bottles. LDPE is resistant to moisture and chemicals, making it suitable for packaging applications.
LDPE is created through a polymerization process in which ethylene molecules bond together to form long chains. This results in a material that is lightweight and has low tensile strength but is highly flexible and impact resistant.
LDPE is easily recyclable, making it a more sustainable choice than other plastics. It can be melted down and transformed into new products, reducing the amount of waste going to landfills.
In addition to its use in packaging and containers, LDPE is also used in the production of plastic pipes and plastic films. Its versatility and cost-effectiveness make it a popular choice for manufacturers in a variety of industries.
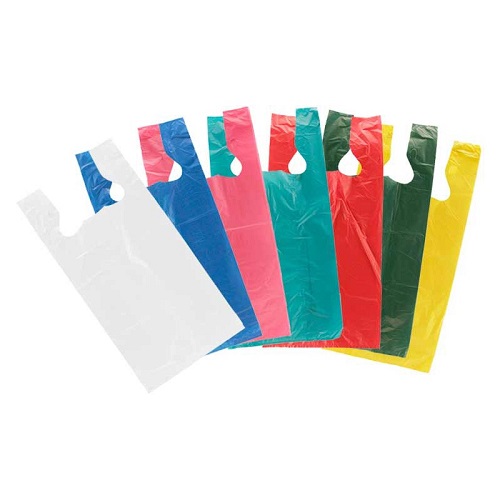
V. Polypropylene (PP)
Polypropylene is a versatile and widely used plastic. It is a thermoplastic polymer used in a variety of applications, from packaging and textiles to automotive components and medical devices.
One of the main characteristics of polypropylene is its high melting point, making it suitable for use in products that require high temperature resistance. It is also known for its excellent chemical resistance, making it ideal for use in harsh environments.
In addition to its physical properties, polypropylene is also known for its recyclability. It can be easily recycled and reused, making it an environmentally friendly choice for many products.
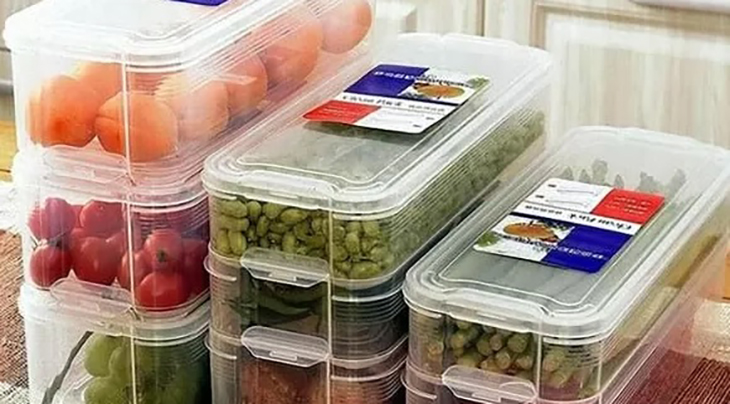
VI. Polystyrene (PS)
Polystyrene is a synthetic polymer that is widely used in many applications. It is a thermoplastic material that can be easily melted and molded into different shapes, making it a popular choice for packaging materials, disposable cups and plates, insulation, and more.
One of the main advantages of polystyrene is its low cost and versatility. It is lightweight, durable, and can be produced in a variety of colors and finishes. It is also a good insulator, making it ideal for use in construction and in thermal and acoustic insulation in homes.
Polystyrene has the disadvantage of low durability, is relatively brittle and easy to break, and is flammable. In addition, because it is used mostly for disposable items, PS plastic accounts for the majority of plastic waste in the environment.
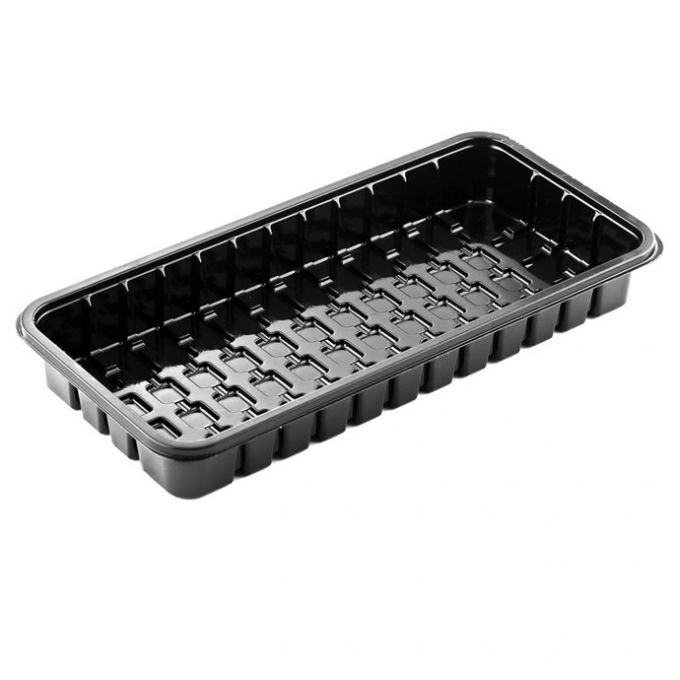
VII. ABS (Acrylonitrile Butadiene Styrene)
Acrylonitrile Butadiene Styrene (ABS) is a popular thermoplastic known for its high durability and good impact resistance. It is widely used in various industries, including automotive, electronics, children’s toys, and
consumer goods.
ABS is known for its impact resistance and toughness, making it an ideal material for products that require high durability. It also has good heat and chemical resistance, making it suitable for a wide range of applications.
One of the main advantages of ABS is its ability to be easily molded and shaped, allowing for the production of complex and intricate designs. It can also be easily machined, sanded, and painted, making it a versatile material for manufacturing.
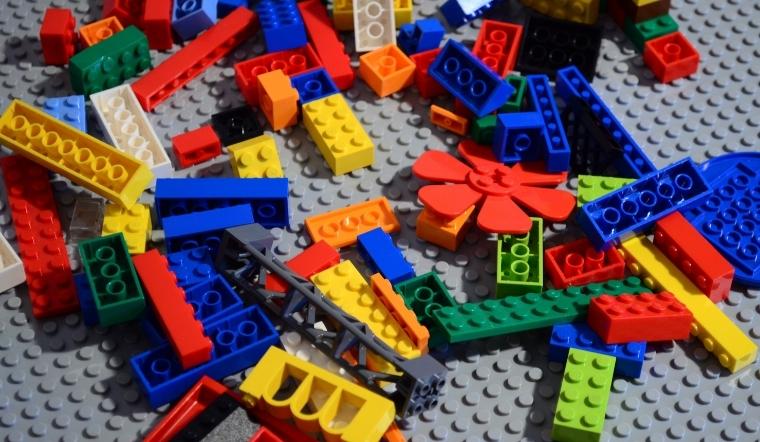
VIII. PC (Polycarbonate)
Polycarbonate is a versatile material that is becoming increasingly popular in various industries. It is a thermoplastic known for its strength, durability, and transparency.
One of the main advantages of polycarbonate is its impact resistance. It is virtually unbreakable, making it an ideal material for applications that require safety. It is commonly used in the manufacture of safety glass, bulletproof windows, and protective shields.
Polycarbonate is also heat-resistant and can withstand high temperatures without warping or melting. This makes it a popular choice for electrical components and automotive parts.
In addition to its strength and durability, polycarbonate is also transparent, allowing maximum light transmission. This makes it a popular material for skylights, greenhouse panels, and even eyeglasses.
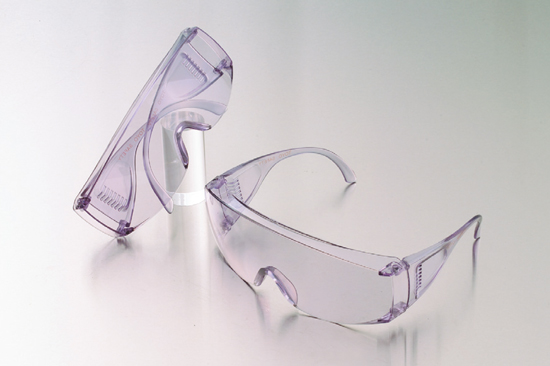