I. What are engineering plastics?
Engineering plastics are a group of plastic materials that have better mechanical properties or thermal resistance than widely used plastics such as PP, PE and PS.
Engineering plastics are designed to meet specific performance requirements, such as strength, high temperature resistance, chemical resistance or electrical insulation properties.
These plastics are commonly used in many industries, including automotive, aerospace, electronics and medical devices. They are designed to withstand harsh environments and demanding applications, making them essential for manufacturing durable and reliable products.
II. Common types of engineering plastics
Here are a few examples of the many types of engineering plastics available on the market. Each type of engineering plastic has its own characteristics and advantages, making them suitable for specific applications in different industries.
1. Polyamide (PA)
PA is a synthetic polymer known for its high strength, toughness, and good resistance to abrasion and impact. PA is also known for its ability to retain its shape and elasticity, making it an ideal choice for products that require flexibility and resilience.
PA is commonly used in the manufacture of automotive parts, medical devices, and sports equipment due to its high performance and reliability. It is also used in the manufacture of gears, bearings, and other mechanical parts.
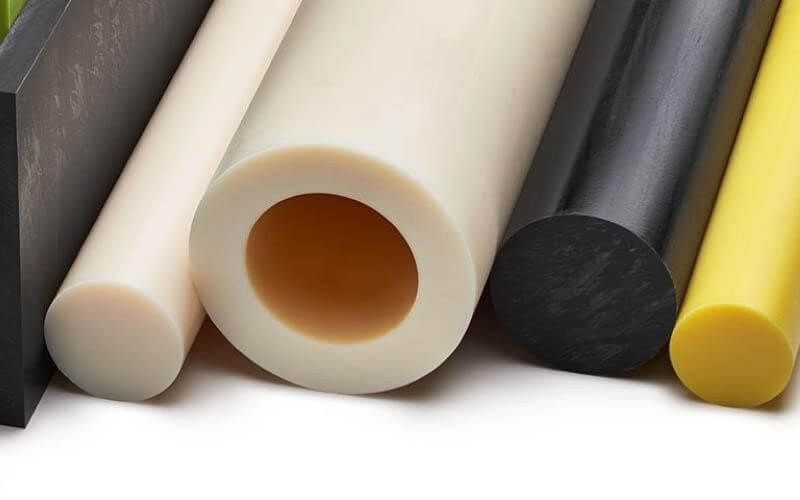
2. Polyethylene Terephthalate (PET)
PET engineering plastic, is a thermoplastic polymer widely used in various engineering applications. It is known for its excellent strength, stiffness, and chemical resistance, making it suitable for many industries including automotive, electrical, and packaging.
PET is commonly used in the manufacture of bottles, containers, and food packaging due to its transparency and high barrier properties. In the automotive industry, it is used for a variety of components such as bumpers, body panels, and electrical connectors.
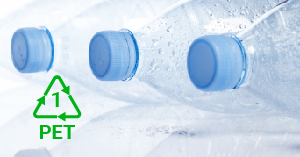
3. Polyetheretherketone (PEEK)
Polyetheretherketone (PEEK) is a semi-crystalline, high-performance engineering plastic known for its exceptional mechanical and thermal properties.
PEEK boasts high thermal dimensional stability, low flammability, excellent chemical resistance, and excellent mechanical properties over a wide temperature range. It is commonly used in the aerospace, aircraft, and automotive industries for structural components that require high load-bearing requirements, such as bushings, gears, shafts, bearings, etc.
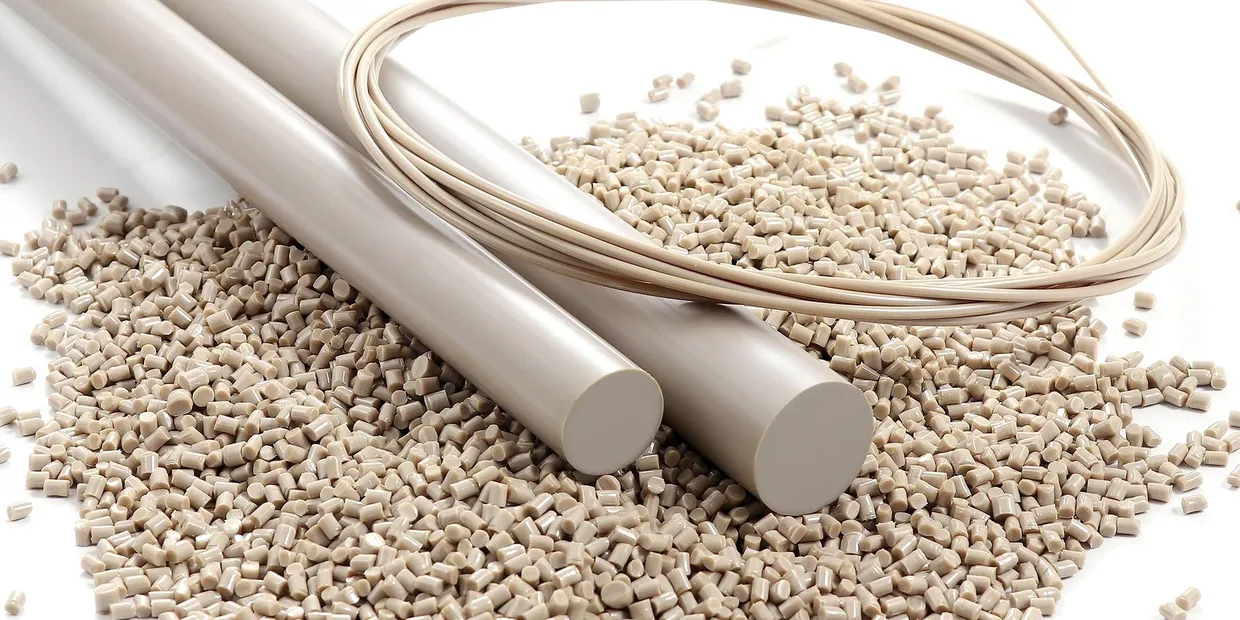
4. Polycarbonate (PC)
Polycarbonate is a transparent engineering plastic known for its high impact resistance and excellent optical clarity and heat resistance, making it a popular choice for products such as eyeglass lenses, safety glasses, and bulletproof windows.
Polycarbonate is also used in the manufacture of electronic components, automotive parts, and medical devices due to its excellent electrical insulation properties and biocompatibility.
In addition, its lightweight nature and ability to be easily molded into complex shapes make it a popular material for consumer goods, such as water bottles and food containers.
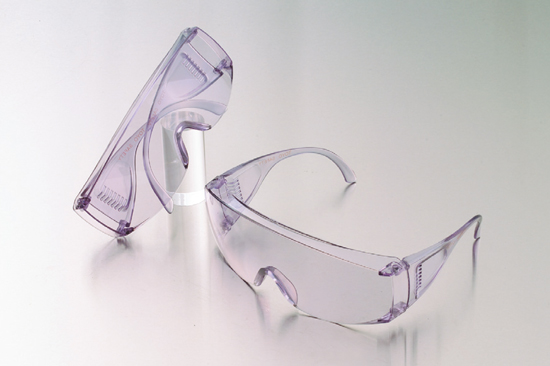
5. Acrylonitrile butadiene styrene (ABS)
ABS plastic is a widely used engineering plastic known for its strength, toughness, and heat resistance. It is commonly used in a variety of applications, including automotive parts, electronic housings, and consumer goods.
ABS is known for its excellent dimensional stability and ease of machining, making it a popular choice for injection molding and 3D printing.
Additionally, ABS can be easily modified with additives to enhance its properties, such as UV resistance or flame retardancy.
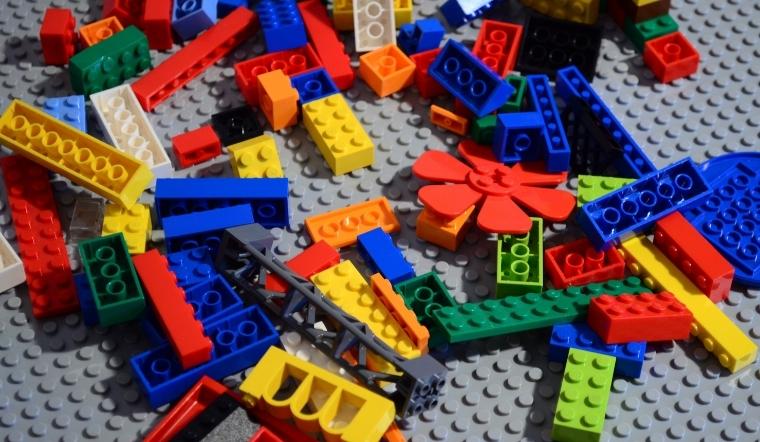