Anti-UV additives play an important role in protecting plastics from the harmful effects of ultraviolet radiation, especially in outdoor applications, exposed to direct sunlight. When plastics are exposed to UV radiation, they can decompose and become brittle, leading to loss of mechanical properties and discoloration. Let’s learn more about anti-UV additives for plastics and their applications in the plastics industry in this article.
I. What are anti-UV additives for plastics?
Anti-UV additives, also known as UV stabilizer additives, are substances added to plastic materials to protect them from the harmful effects of ultraviolet (UV) rays. UV-stabilizing additives work by absorbing or reflecting UV rays, preventing them from breaking down the molecular structure of the plastic, causing it to become brittle, discolored, or degraded; Helps prolong the life and maintain the appearance of plastic products.
II. Types of anti-UV additives
There are many types of UV-stabilizing additives, including UV absorbers, hindered amine light stabilizers (HALS), and quenchers, each with different mechanisms of action and levels of effectiveness. .
A. UV absorbers
UV absorbers work by absorbing UV rays and converting them into harmless heat energy, which reduces the plastic matrix’s absorption of UV rays and thus reduces the rate of weathering.
Each type of plastic needs to use a different UV absorber, for example:
- Phenolic benzotriazoles (UV-360, UV-328) and hydroxyphenyl-triazines (Bemotrizinol) are used for PC resins and acrylics.
- Oxanilides are used for PA and PU plastics.
- Benzophenones are used for PVC resin.
B. Hindered Amine Light Stabilizer (HALS)
HALS works by eliminating free radicals created when UV rays interact with polymers. This helps prevent polymer degradation and can extend the life of plastic products. In addition, HALS also has thermal stability.
HALS are extremely effective when used on POF, PE and PU plastics but they are not effective on PVC plastics.
C. Quenchers
Photo-oxidation can begin with the absorption of light by a chromophore in the polymer (which may be a dye or an impurity) causing it to enter an excited state. This substance can then react with surrounding oxygen, converting it into highly reactive singlet oxygen. Quenchers can absorb energy from excited molecules via the Förster mechanism and then dissipate it harmlessly as heat or lower frequency fluorescent light.
III. Benefits of using anti-UV additives for plastics
One of the main benefits of using UV stabilizing additives in plastics is to prevent yellowing and discoloration. When plastics are exposed to UV radiation, they can discolor and lose their aesthetic appeal. UV stabilizers help maintain the original color and appearance of the plastic, ensuring that it remains visually appealing for a longer period of time.
In addition to preventing discoloration, UV stabilizer additives also help improve the mechanical properties of the plastic. UV radiation can cause plastic to become brittle and lose its strength, leading to cracking and breaking. By using UV stabilizers, the overall durability and performance of plastic products can be enhanced, resulting in a more durable and reliable product.
Furthermore, UV stabilizing additives can also improve the weather resistance of plastics, making them more resistant to environmental factors such as temperature, humidity and pollution. This can be especially beneficial for outdoor applications where the plastic is exposed to a variety of weather conditions.
IV. Application of anti-UV additives in the plastic industry
A. automobile manufacturing industry
When it comes to cars, UV stabilizing additives are often used in the manufacture of exterior parts such as bumpers, panels, and other plastic or rubber parts. These additives help prevent fading, cracking and deterioration of these components, which can occur from prolonged exposure to sunlight.
One of the main benefits of using UV stabilizing additives in car parts is maintaining the aesthetics of the car.
In addition to preserving the vehicle’s appearance, UV stabilizing additives also contribute to the overall longevity and durability of the vehicle. By protecting exterior components from UV-induced degradation, these additives help maintain the structural integrity of the vehicle, ultimately extending the life of the vehicle and reducing the need for Repair or replace regularly.
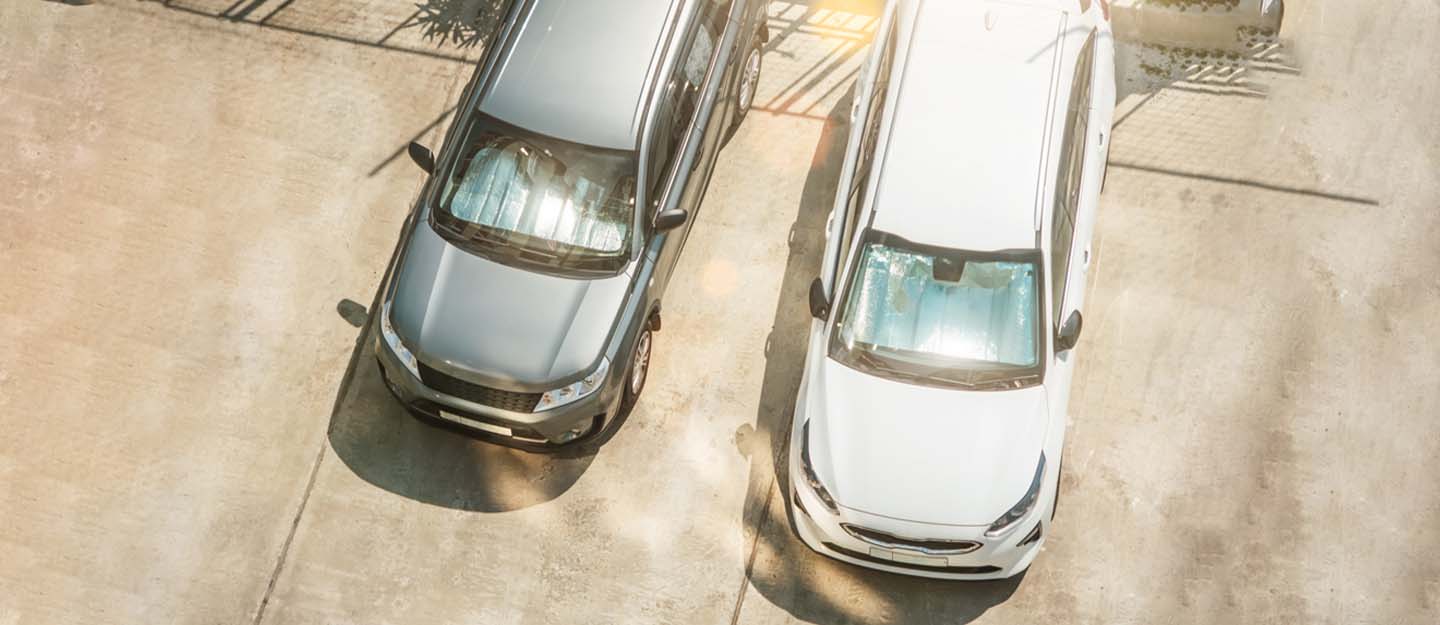
B. Agriculture
UV stabilizer additives are used in the production of agricultural films. UV stabilizing additives are added to these films to protect them from the harmful effects of UV radiation, ensuring they remain effective for longer periods of time. This reduces the need for frequent replacements, saving farmers time and money.
Besides, it also protects plants from the harmful effects of ultraviolet radiation.Ultraviolet radiation can damage plant cells, leading to reduced growth and yield.
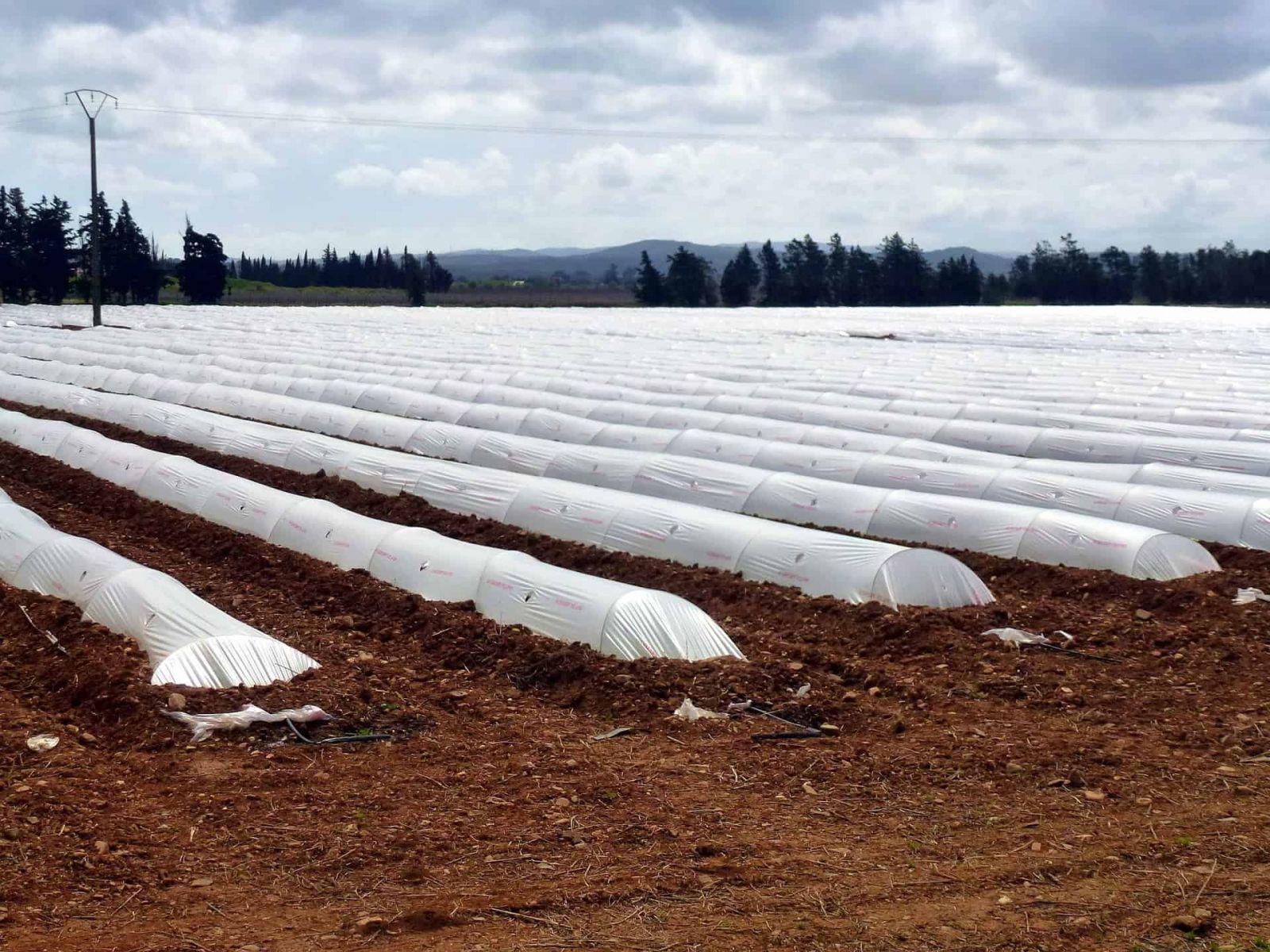
C. Construction materials
UV stabilizing additives are especially important for outdoor construction applications where materials are frequently exposed to sunlight. Without proper UV protection, materials such as plastic pipes and roofing sheets can become brittle, discolored, susceptible to cracking and deterioration.
In addition to protecting materials, UV stabilizing additives also help maintain the aesthetics of building products. By preventing fading and surface degradation, these additives ensure that the material retains its original appearance and performance over time.
By incorporating these additives into construction materials, builders and manufacturers can provide more durable and reliable products, extending the life of the structure.
Application of anti-UV additives to produce plastic roofing sheets.
CPI Plastics Vietnam is the largest direct manufacturer of Masterbatch plastic additive products in Vietnam. Therefore, CPI Plastic is the top choice for factories that need stability in output and quality, to meet the production and export needs of customers.
(Refer to the product here: Anti-UV masterbatch)