Color masterbatch is the most optimal method to color plastic products. Let’s learn about the production process of Color Masterbatch at CPI Plastic Vietnam in this article.
I. Composition of Color Masterbatch
Color masterbatch is a specialized compound made up of 4 basic ingredients: color pigment or dye, base resin, dispersant and additives.
Color masterbatch are divided into 2 types:
- Monochrome: Color particles from a given pigment and supporting resin, wax or dispersion. Contains no additives.
- Customized masterbatch: Has its own formula, mixed with different pigments. Create exact colors according to customer requirements. Additives can be added upon request.
A. Pigments or dyes
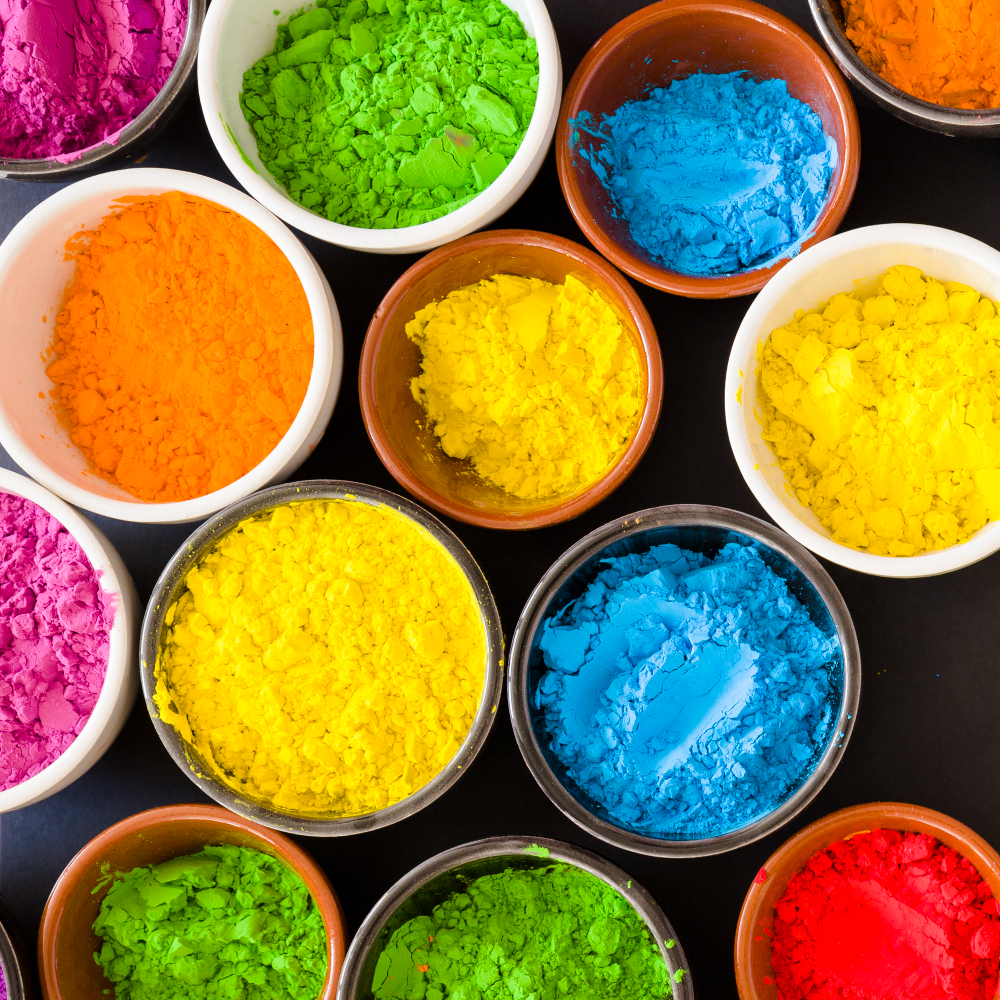
Inorganic pigments: made from insoluble metallic salts or ferrous metal oxides. Inorganic color compounds include artificial inorganic pigments, natural inorganic pigments and natural inorganic colorants. Inorganic pigments include white pigment (Titanium dioxide), black pigment (Black carbon), Cadmium pigment (red, yellow), iron oxide pigment (red, yellow) and other colors.
Organic pigments: Each type of organic pigment has a different structure. Organic pigments include three main types: azo pigments, copper phthalocyanin and dye pigments.
Dyes: There are many types of dyes that can be used to color plastic beads, such as food coloring, rit dye, and acrylic paint. Each type of dye has its own advantages and disadvantages, depending on factors such as desired color, depth, durability, and cost. You can also mix dyes together to create custom colors and effects. However, you should always follow the instructions and safety measures of the dye you are using, and avoid mixing incompatible dyes with each other.
Dyes | Organic pigments | Inorganic pigments | |
Origin | Natural or synthetic | Synthetic | Natural or synthetic |
Relative density | 2.0 – 3.5 | 1.2 – 2.0 | 3.5 – 5.0 |
Soluble in organic solvents and polymers | dissolve | does not dissolve | does not dissolve |
In transparent plastic | Transparent | Blurry / Opaque | Opaque |
coloring ability | High | Medium | Low |
Color brightness | High | Medium | Low |
Light stability | Poor | Medium | Good |
Thermal stability | 170-200oC | 200-260oC | ~500oC |
Chemical stability | Low | Medium | High |
Displacement phenomenon | High | Medium | Low |
B. Base resin
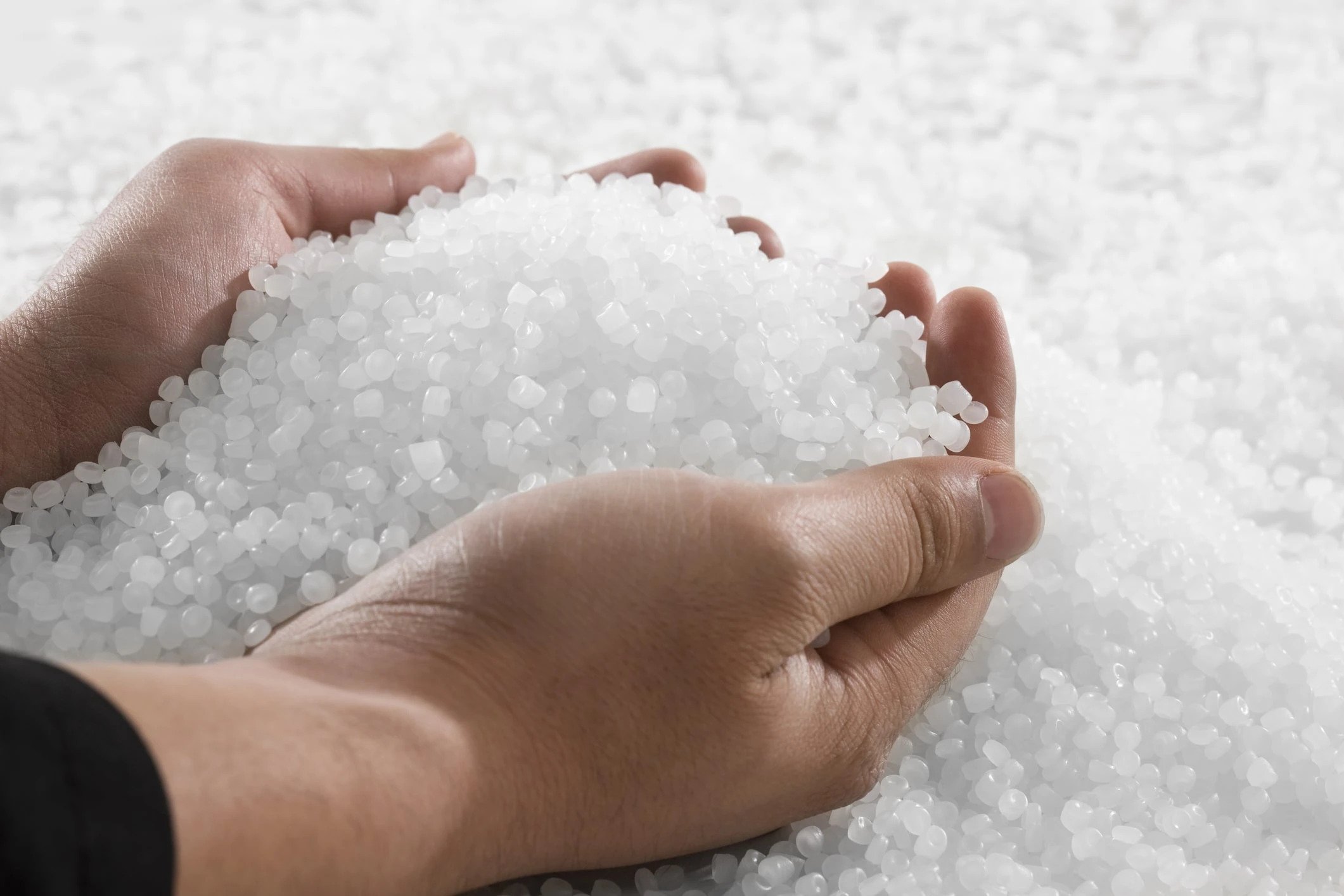
Color masterbatch will usually use PE or PP plastic because these are the two most common types of plastic. In addition, the color masterbatch that is ordered will use the same type of plastic as the product customer want to color. Compatibility will be higher when using the same resin, but consideration can be given based on the fluidity of the base resin.
C. Dispersant
To promote uniform dispersion of pigments and prevent agglomeration, the melting point of the dispersant should be lower than the melting temperature of the resin and have good compatibility with the resin and good affinity for the pigment . The more commonly used dispersing agents are low molecular polyethylene wax, stearate, etc.
D. Additives
Normally color masterbatch will not contain additives. In case of customer request, common additives are often added such as flame retardants, brighteners, antibacterial, antistatic, antioxidant and others.
II. Color Masterbatch Production Process
The masterbatch production process will go through the following 3 basic steps:
- Mix ingredients at high speed.
- Melt the mixture.
- Extruded through mold and cut to form masterbatch.
Currently, colored plastic resins at CPI Plastic are produced using high-speed mixing technology and twin screw extrusion.
First, raw materials (including resins, dispersants, colorants and additives) are fed into the mixer based on the formula. The mixer will mix the material at high speed, through high-speed operation and the role of the baffle to crush the coarse particles of the pigment and pre-wet it with polyethylene wax (which has a relatively low melting point), At the same time, it adheres evenly to the surface of the plastic particles due to friction at high temperature and stirs well to create a flexible surface; The mixture is then fed into a twin screw extruder and melted. The mixture is mixed, milled and completely dispersed, then extruded through a die to form the masterbatch product.
In order for the plastic to have an even color, the pigment particles must be refined to a certain level and evenly distributed into the plastic. Pigment dispersion not only affects the appearance of color products (spots, streaks, gloss, color and transparency), but also directly affects the quality of color products, such as durability, elongation, aging resistance and resistivity.
The size of the pigment particles affects the surface of the product:
- The particle size of the color pigment is larger than 30 microns (μm), there will be spots and streaks on the surface of the product.
- Size 10-30 μm, matte surface.
- When the particle size is less than 5 μm, it can be used for common products without affecting the product’s appearance.
- When weaving filaments (single wire diameter 20-30 μm) and ultra-thin films (less than 10 μm), the pigment particle size should be less than 1 micron.
CPI Plastic Vietnam is one of the largest manufacturers of colored plastic resins in Vietnam. Products of CPI Plastic Company have been exported to more than 80 countries around the world, on all continents. With the motto “OUR PRODUCTS – YOUR SUCCESS“, CPI plastic company always wants to cooperate with all customers to bring Vietnamese products to the world.
If you want to purchase, please contact Hotline: 0913.046.902 for advice and the best price quote.
(See the product: Color Masterbatch)