Currently, plastic is present in almost all fields from life to production. The product is made from diverse plastic, with many eye-catching colors. However, the original material used to make plastic products is virgin plastic that is colorless, transparent or white. So how to dye plastic products? Let’s learn about the two most popular dyeing methods in the plastic industry today in this article!
I. Plastic dyeing using pigment
This is a classification of industrial pigments specifically used for the plastic industry. It is synthesized from chemicals and ground into powder. Powder is mixed with main ingredients during the production process to color the product.
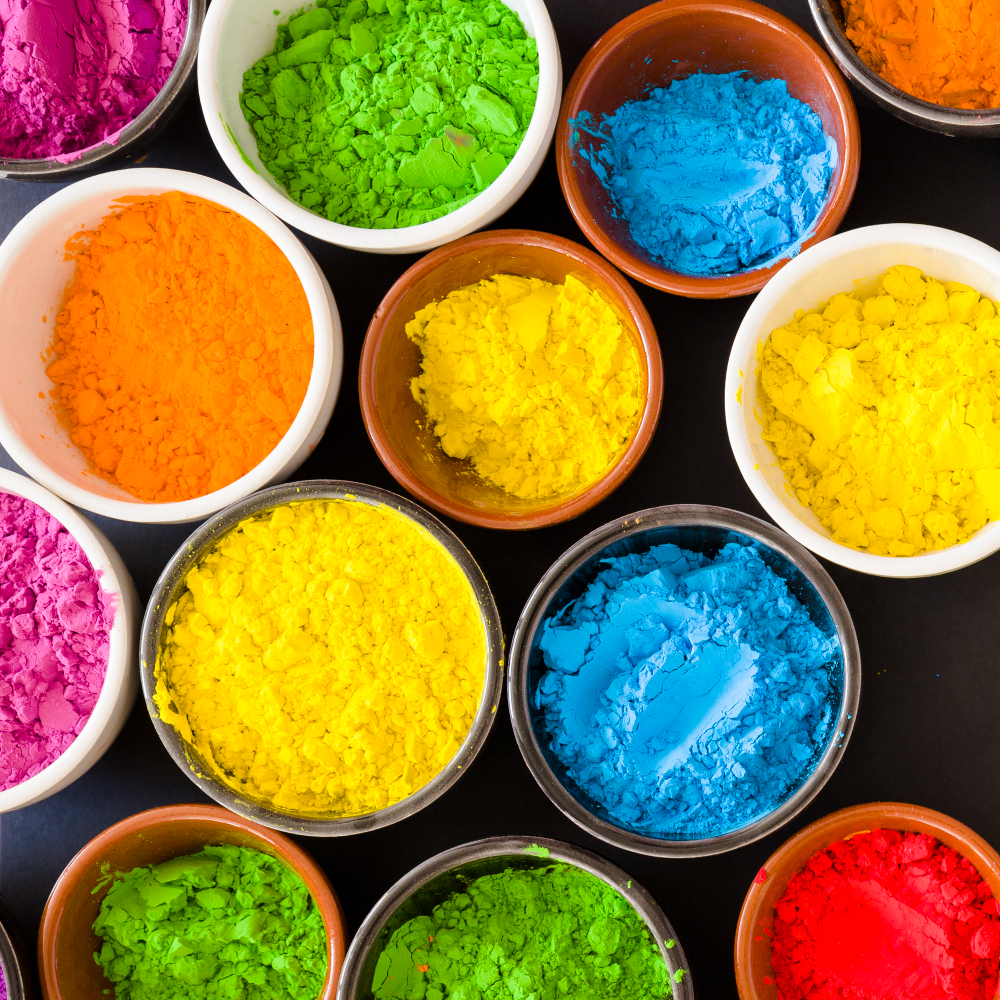
Pigments used in the plastic industry have the following common characteristics:
- The powder form is very dusty and does not disperse completely during the coloring process.
- Cheap price, does not affect the properties of the colored product.
- Easy to process, can be used for all types of plastic.
- You need to be precise when measuring the powder color otherwise it will be easy to get the wrong color.
Pigments are divided into two main types: inorganic pigments and organic pigments. There are also some types of pigments that have other special effects.
A. Inorganic pigments
Inorganic pigments are made from insoluble metal salts or ferrous oxides. Inorganic color compounds include artificial inorganic pigments, natural inorganic pigments and natural inorganic colorants. Inorganic pigments include white pigment (Titanium dioxide), black pigment (Black carbon) and other colors.
Inorganic pigments are more widely used than organic pigments thanks to the following advantages:
- Withstands strong light conditions.
- Resistant to weather influences.
- Good heat resistance.
- Resistant to solvents.
However, because of its high refractive index, inorganic pigments have less bright, opaque colors and weak color intensity.
B. Organic pigments
Each type of organic pigment has a different structure. Organic pigments include 4 popular types: Alizarin, azo pigments, copper phthalocyanin and quinacridone.
Organic pigments have the following main qualities:
- Color quality: Organic pigments are characterized by bright, rich colors. They often have transparent colors but have high color fastness.
- High price: Organic pigments tend to be more expensive to produce, especially synthetic organic pigments. Synthetic pigments require a lot of chemical processing to produce, increasing costs by volume.
- Different light fastness: There are many different types of organic pigments, but most of them tend to retain their color poorly when exposed to light. While some can resist exposure to light and heat well, many will fade over time.
C. Special colors
Besides the two basic types of pigments, there are also a number of other special types of pigments used in special cases.
Fluorescent pigments – Capable of converting UV light into visible colors. Due to the very high level of light reflection, the colors become more vibrant and eye-catching. Often used in toys and packaging.
Nacre pigment – Has a thin flake structure coated with titanium dioxide, which reflects part of the light, creating a shiny feel for the product.
Metallic pigment – Has a fine aluminum flake structure dispersed evenly on the product, creating a sparkling metallic look for the product.
II. Plastic dyeing using color masterbatch
Color masterbatch is a specialized compound used to color plastic. Color masterbatches are prepared from pigments, plastics and other additives through the process of melting, mixing the mixture and then extruding to form pellets.
This is the most commonly dyeing methods in the plastic industry thanks to its outstanding advantages such as:
- High color dispersion.
- Create accurate colors.
- High color fastness.
- Easy to store and transport.
Color masterbatch can be mixed directly into the plastic mixture during the production process; Because the masterbatch mixture contains resin and additives that can affect the properties of the finished plastic, you can rely on it to change the properties of the plastic according to technical requirements. Thanks to these characteristics, colored plastic resins are widely used in products with high quality requirements.
Using colored plastic masterbatch helps optimize production costs and time; It can be mixed directly during the production process according to the manufacturer’s recommended ratio to produce a product with the desired color, without Takes time to mix colors.
Above are the two most commonly used ways to color plastic products. Hopefully through this article you can better understand and make appropriate choices in the business and production of plastic products.
Color masterbatch is produced and distributed directly by CPI Plastic Vietnam. We provide a variety of color masterbatch. In addition, we advise and produce color masterbatch according to exact requirements based on customer samples.
(Refer to the product here: Color masterbatch)
If you want to buy, please contact Hotline: 0913.046.902 for advice and the best price quote.