In the field of plastic production, surely everyone has heard a lot about the phrase Masterbatch. However, many people still do not know what is Masterbatch and how it works. As the industry continues to innovate, understanding the meaning and significance of masterbatch has become increasingly important for manufacturers, and consumers alike. Let’s find out the meaning and importance of masterbatch with CPI Plastic in this article!
I. What is Masterbatch?
Masterbatch is a commonly used term in the plastics industry. It refers to a concentrated mixture of pigments or additives encapsulated in plastic granules. Masterbatch are used in the plastic industry to create color, enhance properties or reduce the cost of producing plastic products.
Masterbatch is a flexible material that can be used in many different industries. It can be customized depending on the intended use as well as the technical requirements of the end product.
II. Ingredients of Masterbatch
The composition of masterbatch usually includes three main components: pigments, additives and base resin. Pigments are responsible for creating color for plastic products. They can be organic or inorganic compounds, depending on the color and desired application. Additives, on the other hand, are substances that help improve the performance or properties of plastics. These may include UV stabilizers, flame retardants, antioxidants, etc. Finally, the base resin acts as a binder, holding the pigments and additives together.
The base material of the masterbatch can be wax or a specific polymer that is identical or compatible with the natural polymer used. For example, masterbatch produced from polymers such as EVA or LDPE can be used for polyolefin and nylon, and polystyrene can be used for ABS, SAN and sometimes polycarbonate plastics. When a different substrate is used and is not compatible with the resin used, the properties of the finished resin will be changed. The usage rate of masterbatch and original resin in normal production is 1–5%.
III. Masterbatch plastic granules
The uses of Masterbatch plastic beads depend on its composition. There are 3 common types of Masterbatch:
Color masterbatch – used to color plastic products. The main ingredients include base resin and colorant. There are also a number of other additives available upon special request.
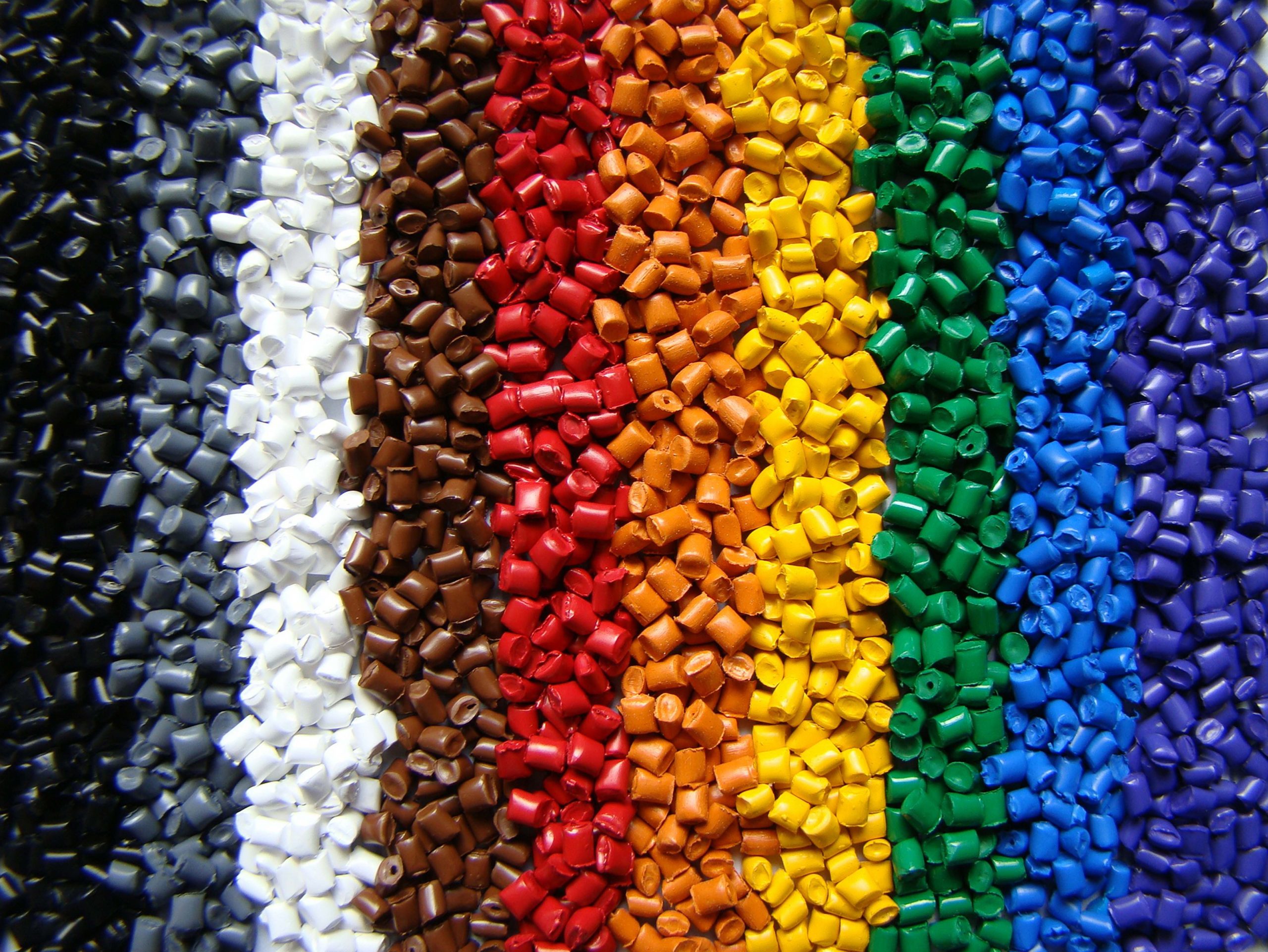
Filler masterbatch – Used to replace part of primary plastic to help cut production costs and help improve some properties of the finished product. Ingredients include base resin combined with minerals (CaCO3, NaSO4, BaSO4, Talc,…) and other additives. Some organic fillers such as bark powder, nut powder, chicken feathers, rice husks… can be used as a substitute for minerals, but are less popular.
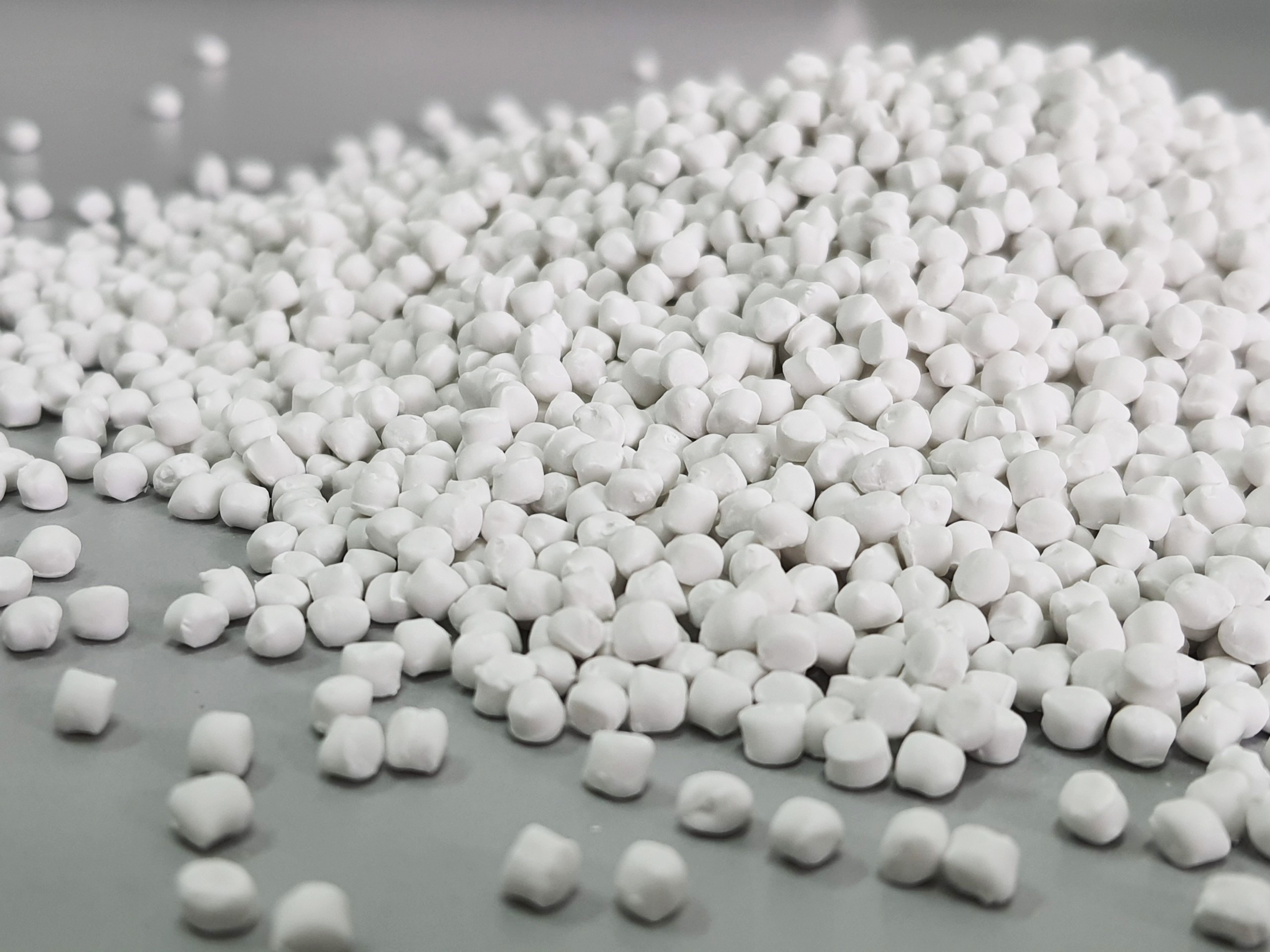
Additive masterbatch – Used to enhance specific properties or functions of plastic products. The main ingredients include base resin and additives.
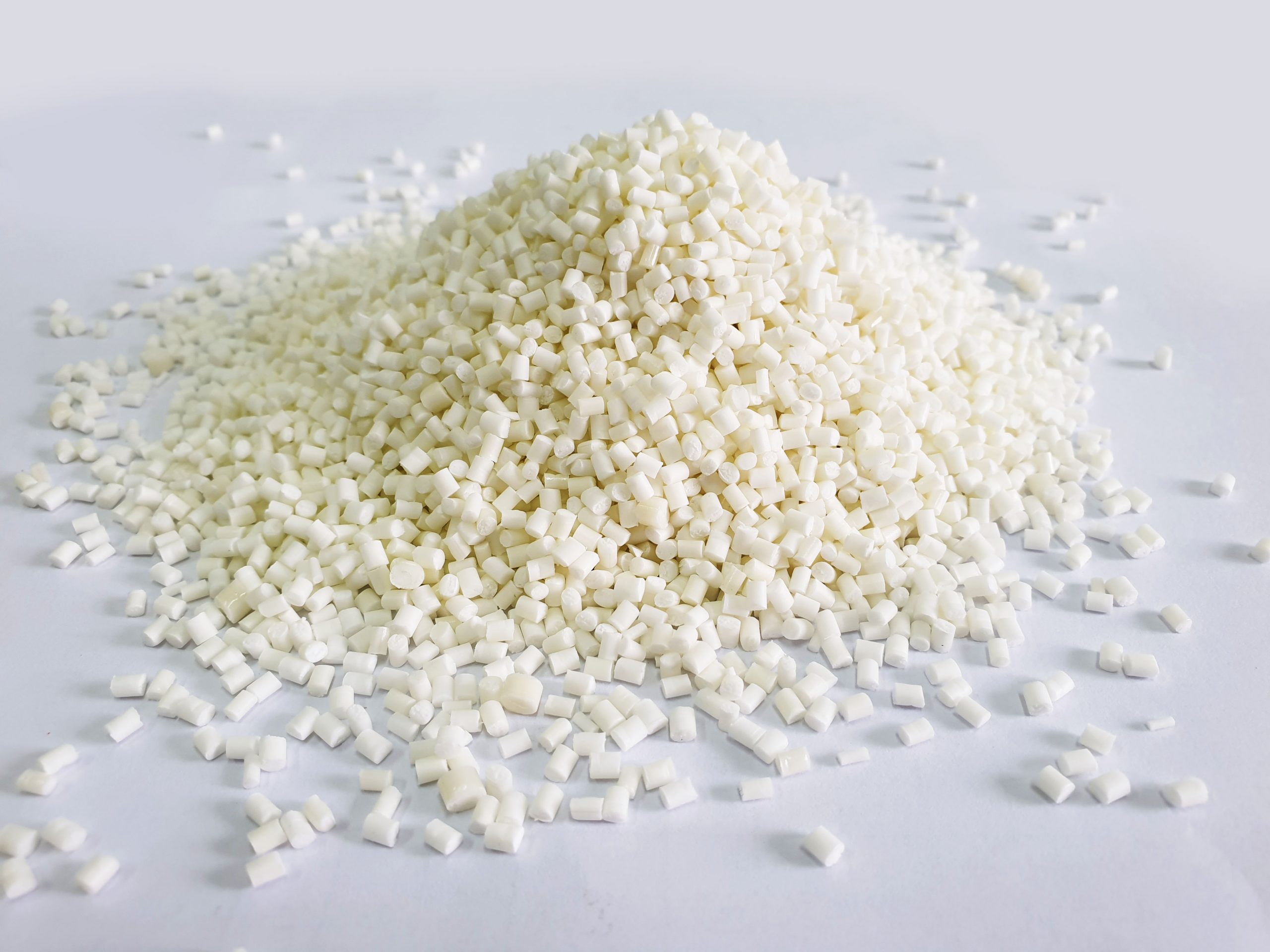
IV. Benefits of using Masterbatch
Masterbatch gives enhanced color and appearance to the final product. By using masterbatch, manufacturers can achieve vibrant and consistent colors, ensuring the final product is visually appealing. Whether it is plastic goods, textiles or even packaging materials, masterbatch can enhance the overall aesthetics of the item.
Second, masterbatch improves processing efficiency. It is designed to be easily integrated into the manufacturing process, allowing for smooth and efficient production. The concentrated nature of the masterbatch ensures that only small amounts are needed, reducing production time and minimizing waste. This efficiency translates into cost savings for the manufacturer.
Since masterbatches are already premixed preparations, their use can alleviate problems of insufficient dispersion of additives or colorants when mixed with raw materials. The dispersion can be further adjusted through the particle size of the masterbatch.
Talking about cost, masterbatch is known for its cost-effectiveness. As mentioned earlier, only a small amount is needed to achieve the desired color or effect. This means manufacturers can save on raw material costs as well as storage and transportation costs. In addition, improved processing efficiency also contributes to overall cost reduction.
V. Masterbatch production process
The general process for producing masterbatch includes the following 4 steps:
- Prepare and weigh the required ingredients according to the recipe.
- Mix the raw materials evenly by heat treatment and extrusion.
- Cool the mixture and spin it into fibers.
- Cut into granules and package the product.
CPI Vietnam Plastics Co., Ltd. is one of the largest Masterbatch manufacturers in Vietnam. Products of CPI Plastic Company have been exported to more than 80 countries around the world, on all continents. With the motto “OUR PRODUCTS – YOUR SUCCESS”, CPI plastic company always wants to cooperate with all customers to bring Vietnamese products to the world.
If you want to purchase, please contact Hotline: 0913.046.902 for advice and the best price quote.